Blog Post < Previous | Next >
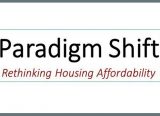
CVP
Paradigm Shift – Part IX: Gen-AI and Factory Built Affordable Housing
The term “efficiency” is in the news these days. However, contrary to the nonsense being peddled by the DOGE crowd, achieving increases in “efficiency,” which is fundamental to increased “productivity” and “wealth creation,” is about much more than randomly firing people to cut costs. If cost-cutting is not done in concert with even greater capital investment in people and technology, the net result is the degradation of operations and a sure path to bankruptcy.
This explains why tech titans -- Google, Meta, Amazon, et al – are simultaneously laying off staff to reduce expenses while investing multiples of those savings in generative AI (Gen-AI) because they know that their investment is the only path to faster, cheaper, better.
Automated manufacturing and rudimentary robotics have been with us for a centuries. However, with generative AI (Gen-AI) we have a technology that can help us design better tools and manufacturing methods… and even better robots.
We can now re-invent manufacturing and question long-held assumptions about how to maximize productivity and reduce costs. We can ask things like, why are production “lines” in a line. Is it more efficient to have products move past fixed “workers” or have “workers” be mobile and able to move to where they are needed most at any given time? Or, if both have mobility and “intelligence,” would a combination of both methods better address manufacturing processes for a particular product?
If the ultimate goal is to increase productivity by optimizing the time spent to manufacture a product, then knowing what is optimal at any given moment (depending on materials availability, production workflow benchmarks, quality assurance standards, etc.) would be the most important question.
Optimizing manufacturing efficiencies and workflow
It’s now pretty much a given that Gen-AI can optimize workflow and resource allocation, in real time, better than any preconceived plan. And we’re starting to see the results of this across many industries.
Multi-functional, articulated arm robots on a Volkswagen production line
Siemens has implemented Gen-AI to optimize its resource allocation. Algorithms analyze supply-chain data, production schedules, inventory levels, and labor availability to optimize work schedules. This ensures efficient use of resources and allows for real-time adjustments in response to unexpected circumstances like supply chain disruptions or equipment failures.
General Electric is using AI-driven predictive maintenance to improve how manufacturing lines handle equipment breakdowns. Their system uses “Internet of Things” (IoT) sensors to collect performance data from operating equipment, to identify patterns indicating equipment deterioration or impending failure. This allows for proactive maintenance, minimizing disruptions, and reducing downtime.
Articulated robotics
Multi-functional, Gen-AI-enabled robots are capable of moving around the production facility and performing an unlimited variety of work tasks (cutting, welding, drilling, nailing, screwing, bolting, grinding, finishing, etc.), as required, working alone or alongside human beings to assist and enhance their capabilities.
This is particularly valuable for housing prefabrication and components construction.
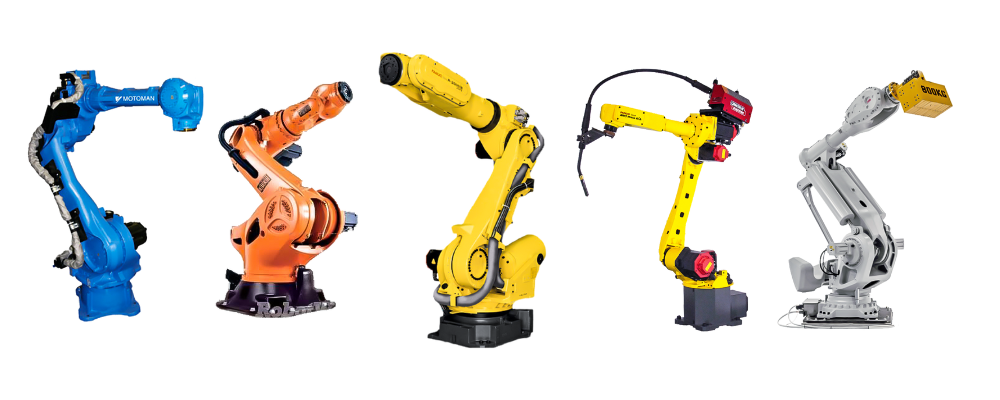
Robots can also work in teams (“cobots”) and optimize manufacturing processes, as needed. And as they “learn from experience” (“machine learning”), their capabilities, efficiency, and ability to re-configure the manufacturing workflow improves. Again, since housing construction is a highly nuanced process (each home design can require the manufacturing of many custom features and layouts), this ability has enormous potential.
The capabilities of Gen-AI enhanced data can create a seamless relationship from product concept to prototyping to supply-chain management to materials sourcing and handling to precision manufacturing and quality assurance to sales, delivery, and installation.
As noted in a report by American Machinist,
“Unlike human workers, robots don’t need breaks and are programmed to focus on a specific tasks. Their focus and resilience enable them to work 24/7 if necessary without interruptions.”
This could have enormous cost-savings benefits to affordable design and development.
Gen-AI and affordable housing manufacturing
We are starting to see small-scale efforts to automate housing construction for modular homes and to manufacture building components, using BIM software-driven robotics. As discussed in Part VIII, these methods integrate and optimize the workflow of project designers, construction managers, subcontractors, and materials suppliers.
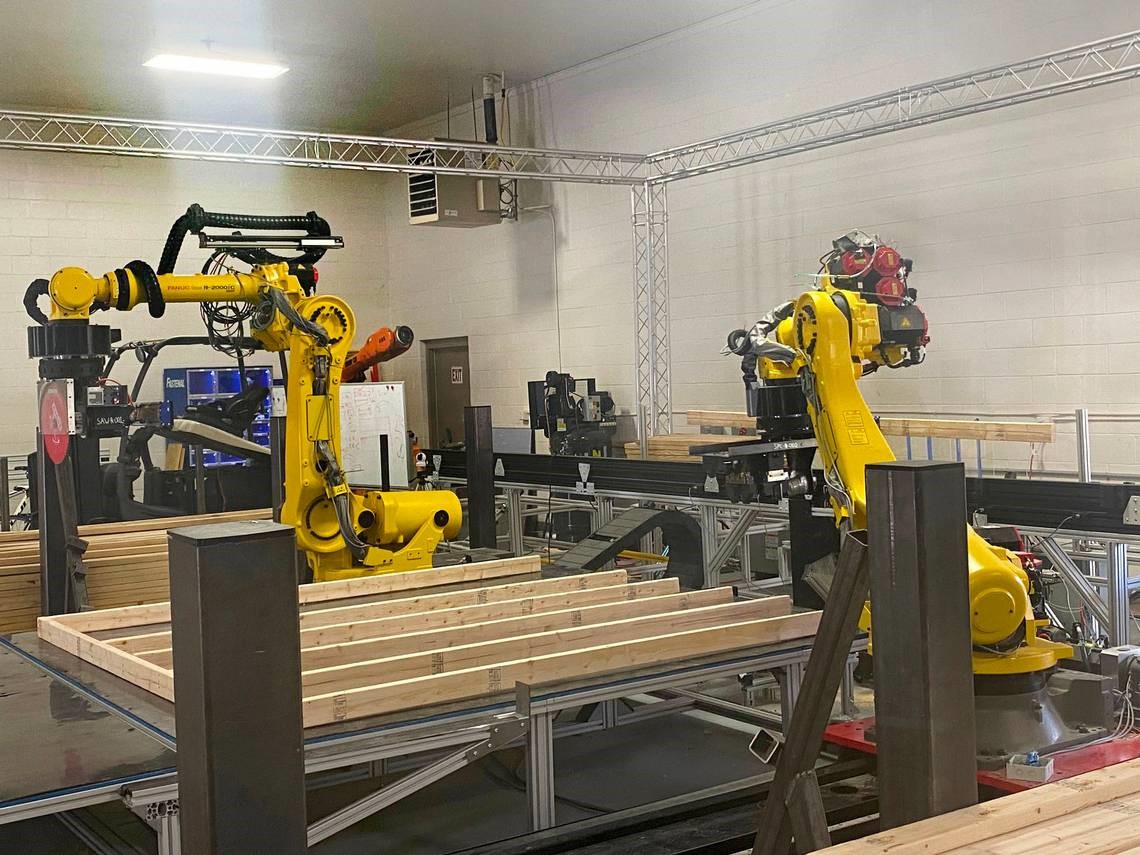
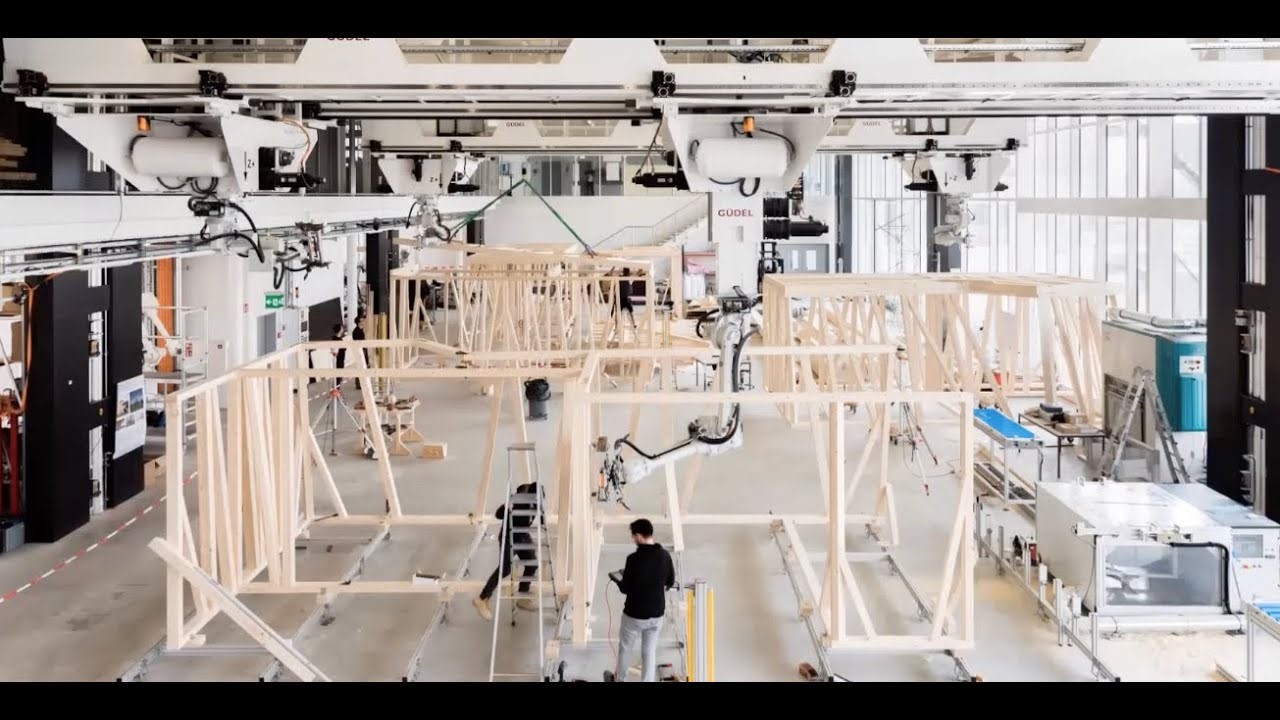
Dfab House, Zurich, Switzerland
But these efforts have barely scratched the surface of what is possible. In addition to the capabilities discussed in “Paradigm Shift - Part VIII: Gen-AI Can Reduce Housing Costs,” some of the manufacturing and construction management process applications of Gen-AI, applicable to affordable housing construction, would include:
Predictive Maintenance: Gen-AI algorithms analyze sensor data from production equipment to anticipate breakdowns, eliminating unexpected equipment failures and down-time. According to Deloitte, predictive maintenance can help reduce breakdowns by 70% and maintenance expenses by 25%. (Source: Deloitte)
Quality Control: Gen-AI-driven inspection, using computer vision tools ensures high construction standards.
Workflow Optimization: Gen-AI monitoring and analysis of real-time data automatically alters manufacturing schedules and processes, identifies bottlenecks, enhances efficiency, reduces waste, and streamlines overall production.
Resource Allocation: Gen-AI monitors supply chain data, materials and products inventory, construction schedules, and labor availability and can ensure efficient use of resources and balance supply and demand to cut costs and conserve resources.
Gen-Ai can even determine the best way to cut custom-sized shapes out of sheets of plywood for maximum yield, even if the shapes of the pieces needed are different for every sheet.
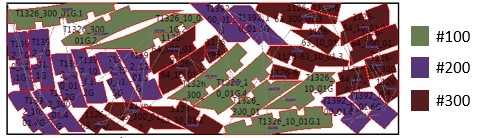
Plataine
Construction Scheduling: Gen-AI can analyze variables and provide contractor, subcontractor, and materials delivery schedules that are coordinated with availability, job site weather, traffic, and other job site circumstances.
Trouble-shooting: Gen-AI can provide real-time insights and recommendations when manufacturing or project coordination issues arise. It has instant access relevant specifications, codes, and industry standards, on the fly, to resolve conflicts, streamline construction, and reduce errors that lead to expensive change orders.
According to a report published by Accenture, applying Gen-AI, in general, to prefabrication and manufacturing of any product will dramatically increase profit margins.
But you can’t get there from here
The capital investment required to bring the housing construction business into the 21st Century will be daunting. So, where will it come from?
As it stands, it will all have to come from private capital. But there are only a handful of housing development companies currently operating at sufficient scale to even begin to justify such large, long-term investments. And, since housing, unlike almost any other manufactured item, is and will always be essentially a locally sourced product, it suggests that multiple manufacturing facilities will be needed in proximity to large potential markets near major population centers and major transportation hubs.
However, major homebuilders are already financially stretched and sitting on large inventories of unsold homes due to high mortgage rates, so any renaissance in home building technology and manufacturing will undoubtedly need a concerted tax and public policy effort, as well as financial assistance from federal and state agencies.
Considering the state of “government” at the moment, I’d say, good luck with that.
Though the need for housing that is actually affordable is acute in California, the Department of Housing and Community Development (HCD) and our elected representatives in Sacramento seem to be stuck in a state of profound cluelessness: chasing each other’s tails, bereft of creative ideas, wandering in a fantasy world of housing quotas (homes that will never be built), doubling down on blame and shame and punishment and penalties and mired, beyond redemption, in a counterproductive and, frankly, moronic morass of identity politics.
California’s governance has become an absurd, virtue-signally ship of fools.
And the bottom line is that after two decades of aggressive California state housing policies we have failed to put a dent in the need for truly affordable housing. We are now, actually losing older, existing affordable housing faster than we are replacing it.
At the local level, severely cash-strapped counties and cities tinker with meaningless little grants and loan interest rate schemes derived from minuscule, local “housing funds,” while trying to float more and more bonds and other forms of unsustainable public debt and ratcheting up special “services” charges and processing fees on residents, or by proposing idiotic ideas like asking desperately under-funded school districts to be guarantors of super, high-risk, project-based, housing bonds!
And then there’s the federal government, where the bulk of the financial assistance and policy guidance would need to come from. But, what are the odds of that?
In my opinion, for the foreseeable future, any leadership in housing from Washington, D.C. is hopeless because their economic ideology violates the fundamental principle that cutting costs must go hand in hand with commensurate investment to increase productivity and build wealth or not just it’s doomed to fail, but it will only make matters even worse.
At a time when D.C. should be doubling, no, tripling down on investing in and incentivizing massive capital investment in research and development of Gen-AI affordable housing construction technology, they are lost in zero-sum thinking and political power grabs.
Yet another opportunity and moment in time that will be missed.
Coda
The Paradigm Shift series has attempted to take a comprehensive, but by no means exhaustive, look at the challenges to housing affordability. This has included an analysis of what contributes to the “un-affordability” crisis in our lives, the history of housing design and development, and the public policy initiatives and blunders, past and present, that have brought us to where we are today. In the course of doing that, I’ve focused on looking to the future and suggesting how we might better address these challenges going forward.
I hope you’ve found it helpful.
Community Venture Partners remains committed to advocating for and finding ways to realize affordable housing solutions through collaborative, public-private partnerships and initiatives.
For more, see;
Paradigm Shift: Rethinking Housing Affordability
Paradigm Shift - Part II: Housing Unaffordability May Be Just Beginning
Paradigm Shift - Part III: How Affordable Housing Need Powered the Modernist Movement
Paradigm Shift – Part IV: The Assault on the American Dream
Paradigm Shift - Part V: Automation and AI, Double-edged Swords for the Housing Industry
Paradigm Shift - Part VI: New Hope for Affordable Housing?
Paradigm Shift - Part VII: Faster, Cheaper, Better
Paradigm Shift - Part VIII: Gen-AI Can Reduce Housing Costs